COMMITTED TO
ENVIRONMENTAL
PROTECTION
RESPONSIBLE PERFORMANCE
Our ambition is to prioritize and allocate resources to unlock new levels of performance and sustainability in our operations and thel products we make.We strive to create specialized fabric solutions that positively impact people andthe planet by simultaneously increasing the durability of our products andminimizing the resources we consume.The DEEPBLU Fabrics ResponsibilityUpdate outlines the challenges and our steps toward this better way of business.
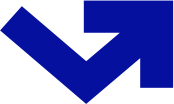
SUSTAINABILITY PILLARS
REDUCING OUR CARBON FOOT PRINT
REDUCING OUR WATER FOOT PRINT
REDUCE AND RECYCLE CHEMICALS
CERTIFICATION AND RESPONSIBILITY
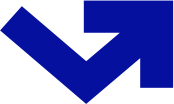
As of 2024, our energy consumption per unit has achieved a 39% reduction compared to the baseline year (2019). In line with our sustainable development roadmap, we plan to phase out liquefied petroleum gas and natural gas-fired boilers by 2030, transitioning completely to electricity and steam-powered energy systems. This energy transition is projected to deliver an additional reduction of over 10% in specific energy consumption upon full implementation.
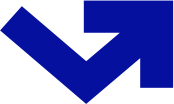
We have implemented an intelligent water stewardship system across production processes, achieving water-use efficiency that substantially outperforms industry benchmarks through innovative technological upgrades and closed-loop water circulation. Monitoring systems for dynamic water optimization, we ensure precision in resource allocation. For solvent-containing wastewater, multi-stage purification and regeneration units enable efficient solvent recovery and advanced water treatment, establishing a full lifecycle water reuse framework that continuously enhances liquid resource utilization efficiency.
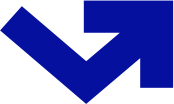
We employ industry-leading solvent recovery systems and Regenerative Thermal Oxidizer (RTO) technology, innovatively integrating spray absorption and thermal combustion into a unified high-efficiency treatment solution. The spray module utilizes high-efficiency packed towers for three-stage gradient purification of water-soluble components in exhaust gases. The resulting organic waste liquid is transported via an intelligent transfer system to a centralized distillation facility for purification and reuse. The treated exhaust gas undergoes parameter optimization through an intelligent temperature-humidity control system before entering the RTO unit for high-temperature pyrolysis at 850°C. Notably, the DMF solvent recovery rate exceeds 99%, setting a new industry benchmark.
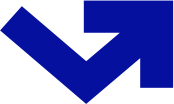
As an industry-leading sustainable manufacturer, we have established a comprehensive international certification framework:
Eco-Certifications: Bluesign® System Partner, Global Recycled Standard (GRS) 4.0, Oeko-Tex® Standard 100 Class IV
Social Responsibility: Higg FEM VERIFICATION
Management Systems: Triple certifications in ISO 9001 Quality Management, ISO 14001 Environmental Management, and OHSMS 18001 Occupational Health & Safety
This certification matrix spans the entire value chain from raw material traceability to production processes and employee rights, demonstrating our global leadership in sustainable manufacturing.
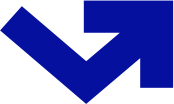
ENVIRONMENTAL CERTIFICATE
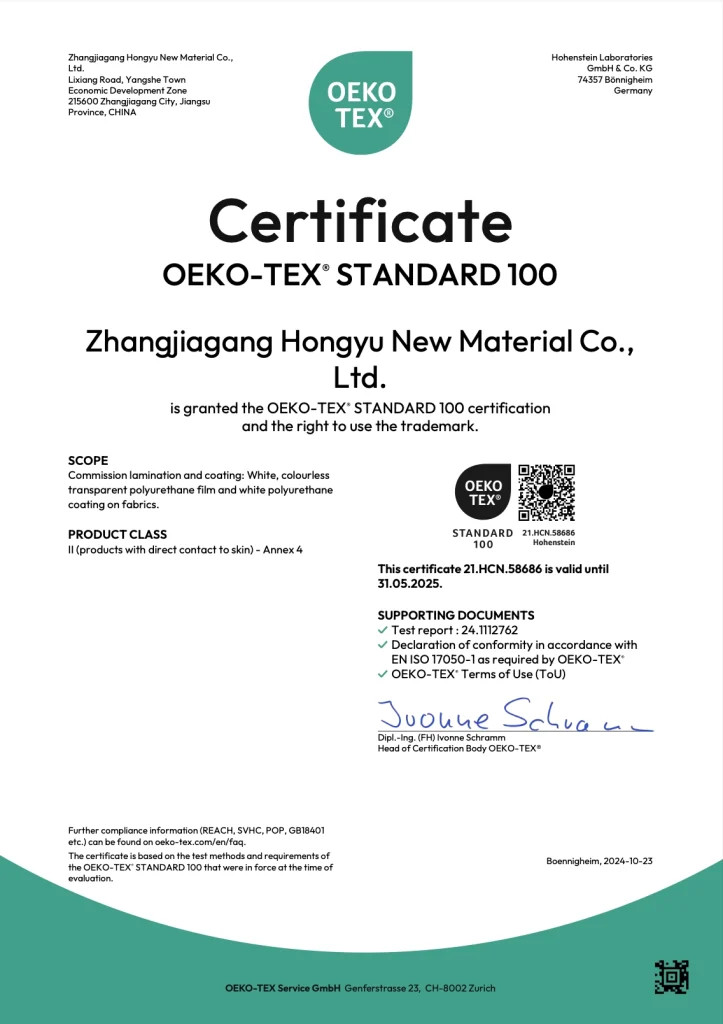

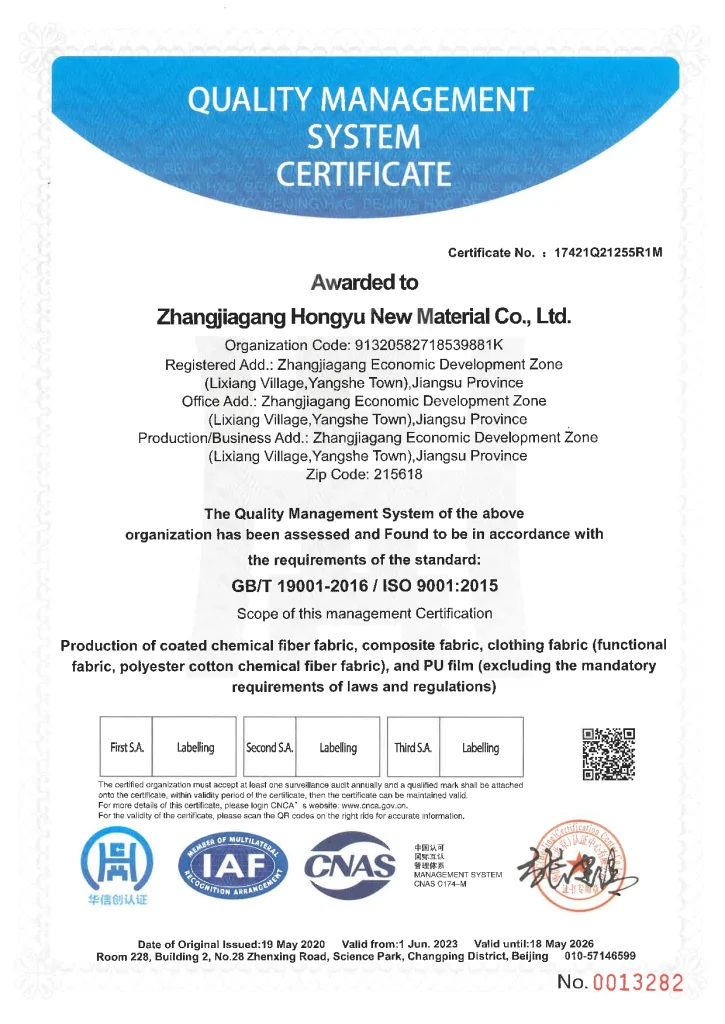
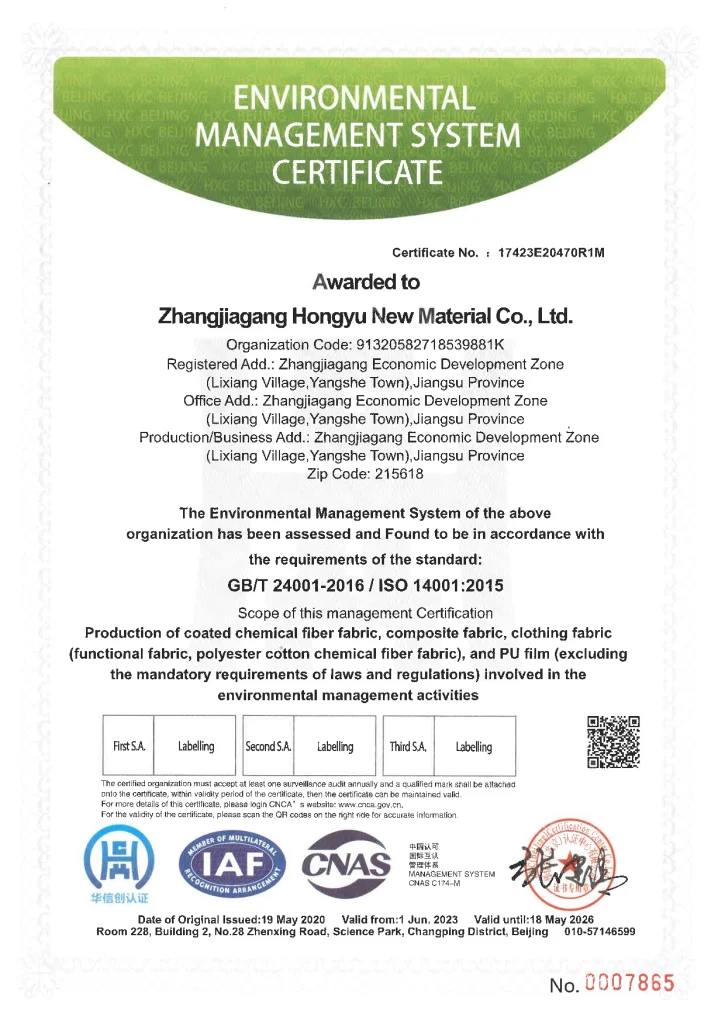
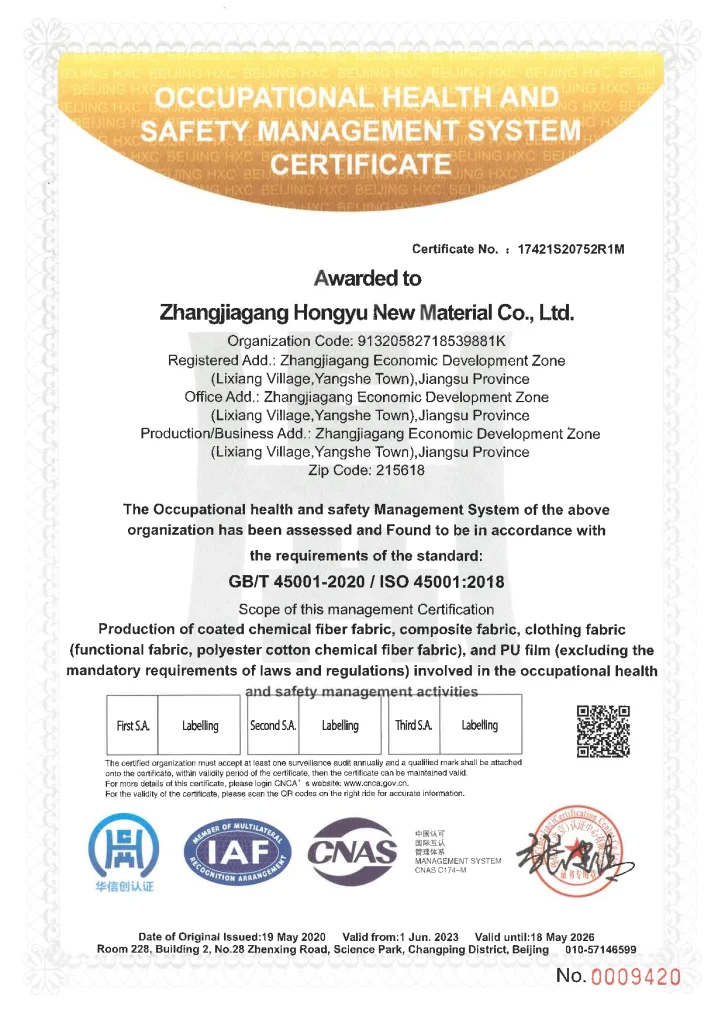
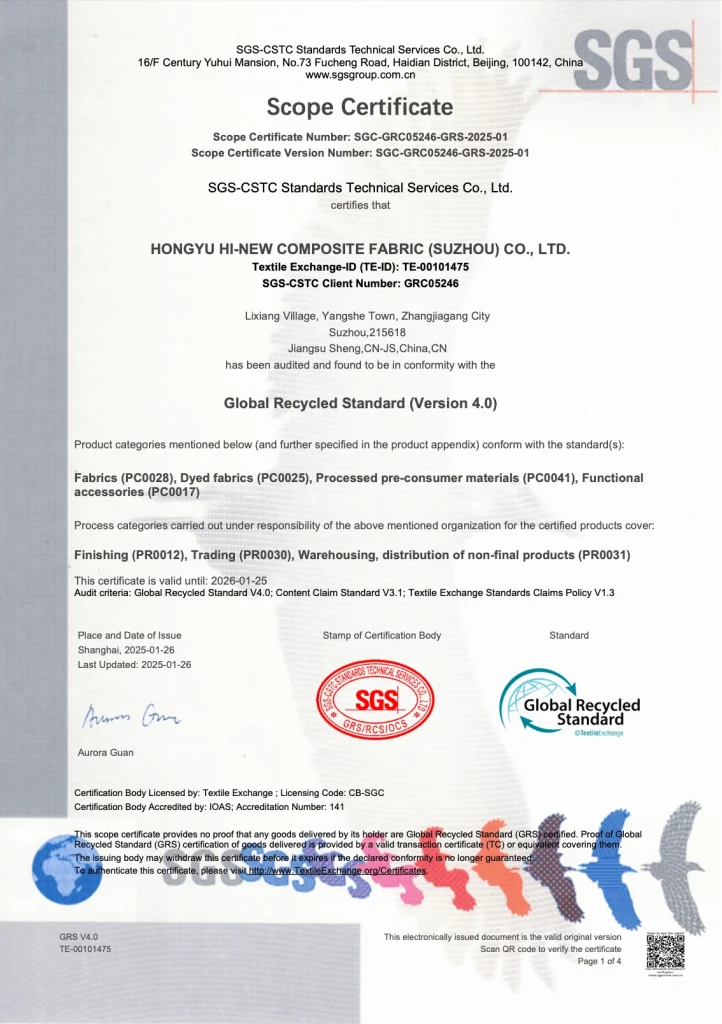
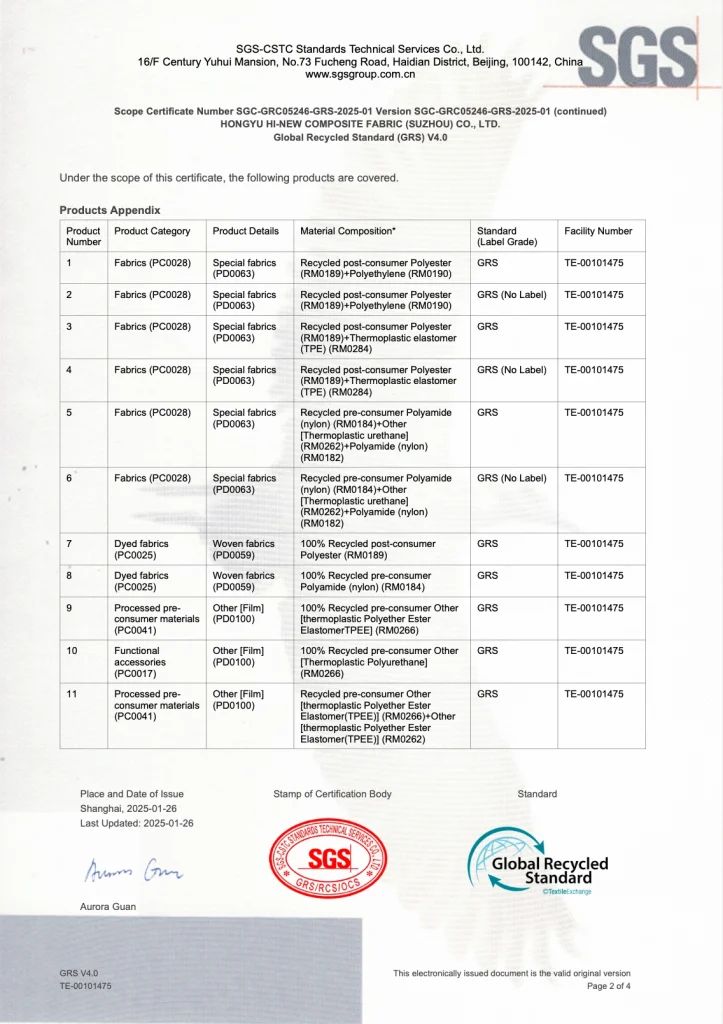
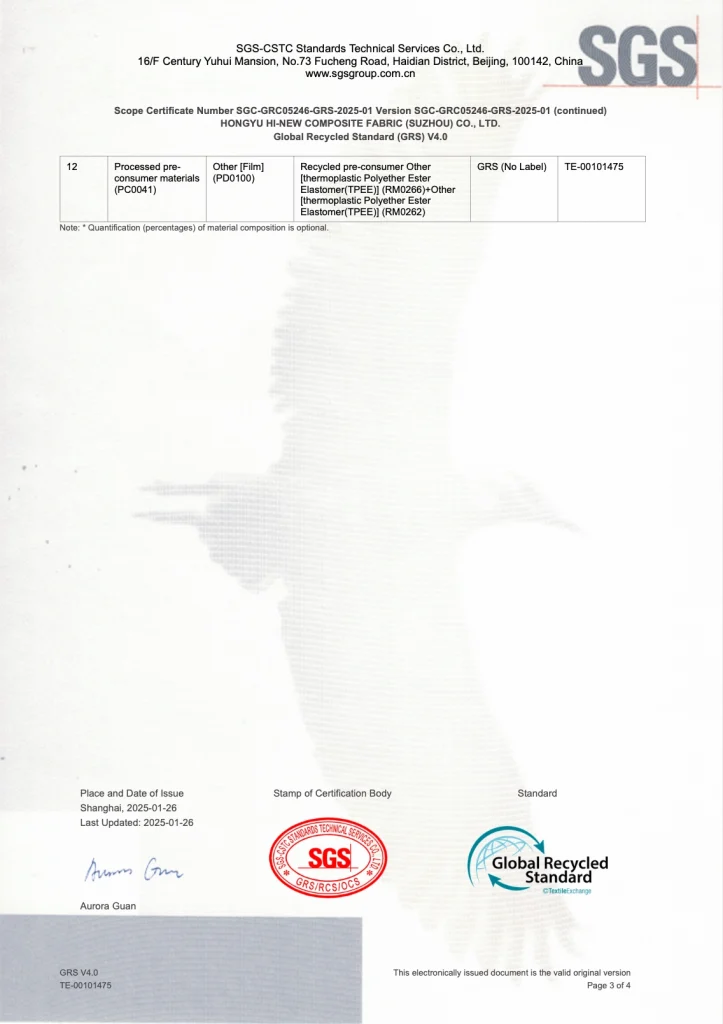
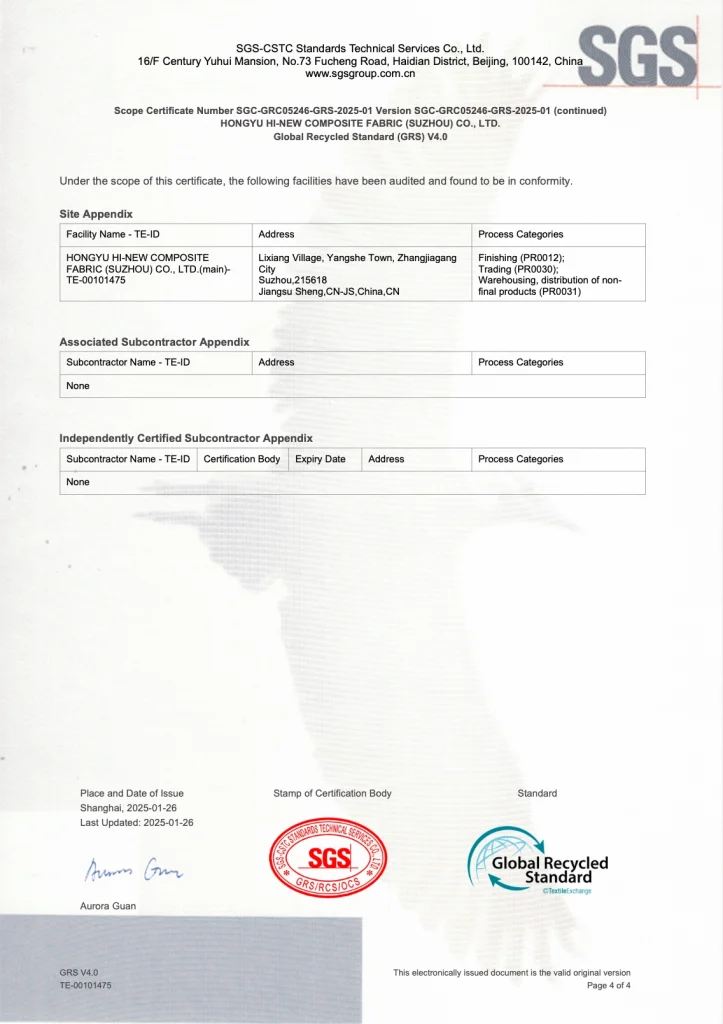
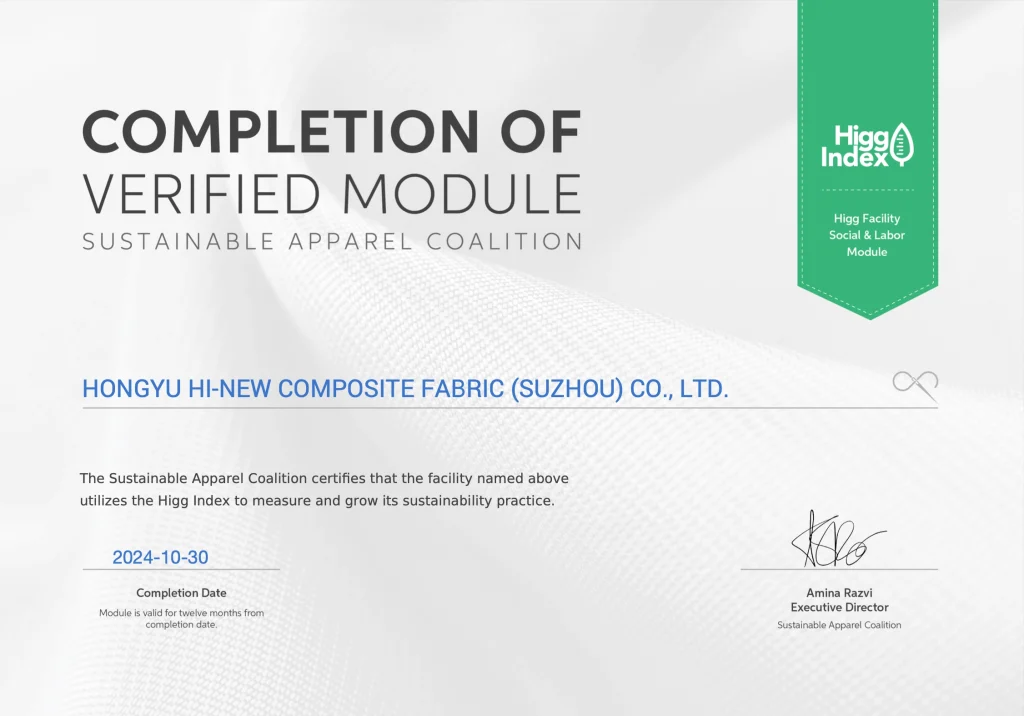